Grain Elevators and the Explosion Problem
Grain elevators come in all sizes and shapes. Some are connected to processing facilities, others serve only as bulk storage. Bulk storage facilities are often grouped into three functional categories that roughly correlate with their size: country elevators (the smallest), inland terminals, and export terminals (the largest).[3] Differences in function, prod-
uct, and capacity have all been urged as reasons for avoiding safety standards of general application. Feed mills, for example, have a much better safety record than bulk grain storage facilities.[4] Some "country elevators" handle grain only a few days a year, obviously minimizing the opportunities for accidents. The significance of these distinctions for safety regulation is unclear because throughput—the amount of grain moved through a facility—has a more direct bearing on safety than function or capacity.[5]
The Explosion Problem
Of all the hazards associated with grain handling, the most serious one is also the most difficult for those outside the grain business to understand. It is grain dust. This dust, generated whenever grain is handled, is easier to ignite and results in a more severe explosion than equal quantities of TNT. One insurance company distributes placards with the warning "Grain dust is like high explosives." Dust explosions account for the vast majority of personal injuries and property losses in grain-handling facilities. There are thousands of small fires in these facilities every year; estimates range from 2,970 to 11,000. But the twenty to thirty explosions a year account for almost 80 percent of the property damage and 95 percent of the fatalities[6] (see table 4). Making sense of these trends over time is complicated by the changing fortunes of the grain trade. The major explosions in 1977–78 coincided with tremendous increases in wheat exports (primarily to the Soviet Union). The comparatively low number of explosions in recent years, on the other hand, is attributable in part to decreases in grain sales.[7] Fluctuations in trade patterns notwithstanding, the explosion problem remains the most serious hazard in grain elevators.
Contrary to popular belief, explosions in grain elevators are not caused by spontaneous combustion. To cause an explosion, the dust must be mixed with air to form a dense cloud. (Layered dust only smolders upon ignition.) The airborne dust concentrations must also be above the lower explosive limit (LEL), a condition so opaque that visibility is minimal and breathing is difficult. Concentrations above the LEL occur regularly inside most bucket elevators (described below) but seldom elsewhere in a facility. Also contrary to popular belief, grain elevator explosions are not one big blast. They usually involve a primary explosion and a series of secondary ones.[8] The primary explosion generates shock waves throughout the elevator, often raising into sus-
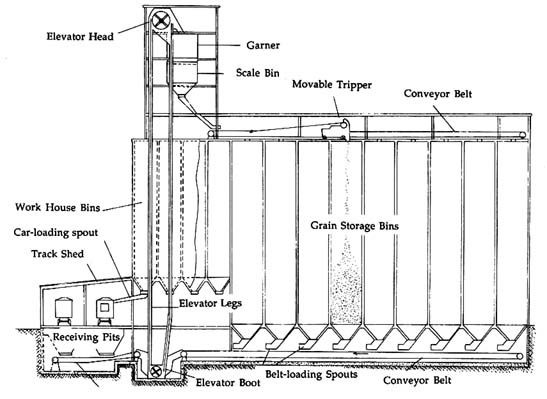
Figure 1. Terminal-Type Grain Elevator
|
pension layered dust on walls, rafters, equipment, and the floor. Accumulations of as little as one-hundredth of an inch will propagate the flame from an initial explosion. In other words, layered dust provides the fuel to turn a primary explosion—often itself quite minor—into a major one.
There are two basic schools of thought about how to approach the explosion hazard: one, eliminate ignition sources; two, control airborne and layered dust. Although it seems obvious that neither strategy should be pursued exclusively, the debate over safety standards is often between groups that have a strong preference for one approach.
The Ignition-Control Strategy
Industry's inclination, according to a former USDA investigator, is to concentrate on ignition sources. Ignition occurs most frequently in the bucket elevator—a continuous conveyor belt with equally spaced buckets (often metal) that elevates the grain and discharges it into a spout (see figure 1). The top section of a bucket elevator, where the drive is
located, is referred to as the "head." The bottom section, where grain enters the elevator, is known as the "boot." The "leg" connects the head and the boot.
Ignition sources are varied and often notoriously difficult to pinpoint. In a study of fourteen explosions, the USDA identified ten different "probable sources," the largest group (four) being "unknown."[9] Most studies agree that welding or cutting (also known as "hot work") is the largest known ignition source, accounting for perhaps 10 to 20 percent of all explosions. Other common ignition sources include electrical failure, overheated bearings, foreign metal objects sparking inside the leg, and friction in choked legs. "Jogging the leg"—trying to free a jammed bucket conveyor by repeatedly stopping and starting the driving motor—is a primary cause of friction-induced explosions.
Ignition-source control can take several forms. One is mechanical. Mechanisms including electromagnets and special grates can minimize the problem of metal objects entering the grain stream. Belt speed, alignment, and heat monitors can be used to detect hazardous conditions and shut down the equipment before suspended dust is ignited. The effectiveness of these devices varies, but quality has improved since their introduction to the grain-handling industry ten or fifteen years ago. Another approach to ignition control is behavioral. Employees are instructed not to jog the legs. Rules against smoking are strictly enforced. Permit procedures are instituted to ensure that hot work is done safely, and preventative maintenance schedules are instituted and implemented.
Whatever the combination of mechanical and behavioral requirements, ignition-source control has two limitations. First, there are countless potential ignition sources. The National Academy of Sciences (NAS) has reported the results of two surveys in which the ignition source remained unknown in over half the cases. Virtually every piece of equipment, as well as every grain transfer point, is a potential ignition source. Eliminating or controlling them all seems impossible. Second, as an NAS panelist put it, "ignition control is fine if you have perfect people; but people will make mistakes and then the equipment fails." A common example is jogging jammed conveyors instead of inspecting and digging out the elevator boot. This problem has been recognized for years, yet it persists largely unabated. According to an insurance representative, operators of some country elevators encourage this time-saving but risky practice. In short, everyone agrees that good operating procedures are a good idea. They are also inherently
difficult to enforce. Since operational breakdowns are inevitable, critics consider this loss control method inadequate by itself.
The Housekeeping Strategy
The other school of thought about grain elevator safety is enamored of—some say preoccupied with—"housekeeping" (or dust control). The label can be misleading to the extent that it conjures up only images of brooms and vacuum cleaners. Dust control is aimed at both airborne and layered dust. Airborne dust can be removed by various systems of aspiration, also called pneumatic ("moved or worked by air pressure)" dust control. Pneumatic dust-control systems have four major components: hoods or other enclosures; ductwork; a filter, or dust collector; and an exhaust fan. Layered dust can also be removed automatically, but in all but the largest facilities it is removed manually: with vacuum cleaners, brooms, compressed air, and, in some cases, water.
Both types of housekeeping (pneumatic dust control and layered dust removal) are controversial, but in the first case the disagreement is mostly technical, while in the second it is largely a matter of economics. The technical potential of pneumatic dust control is highly disputed. One grain elevator insurance company touts a system it claims can reduce dust concentrations in the bucket elevator below the lower explosive limit. The technology was not proven to the satisfaction of a 1982 NAS panel, but panel members placed a high priority on continued research in this area.[10] Many in the industry still consider such technology unavailable. Others claim to have used it successfully.[11] Both are probably right, as the design of pneumatic dust-control systems is, according to a Cargill engineer, "more of an art than a science." Engineers cannot simply take specifications for the desired concentration of airborne dust (or rate of accumulation for layered dust) and design a system that will perform accordingly. The technology for removing airborne dust is too uncertain. Much depends on how the system is installed and maintained.
Layered dust poses much less of a technical problem. How to remove it effectively is not very controversial (although the virtues of vacuuming versus sweeping are a minor topic of disagreement). For large facilities, dust removal is usually part of normal operations. Sweeping is done at least once per shift at all export facilities. But for many smaller facilities, removing layered dust means hiring additional labor and slowing down operations when they are most profitable. Few quarrel
with the conclusion of the NAS that housekeeping and maintenance are often given low priority and are usually the first tasks postponed when there is a rush of business.[12] A grain company representative on the NFPA Technical Committee on Agricultural Dusts concurs that "there are many, many filthy ones that get by." A less tactful USDA investigator describes the prevailing levels of housekeeping in grain elevators as "fair to abysmal." The main objections to stricter housekeeping rules is the cost. The controversy, in short, is managerial, not technical.
Trying to estimate the number of "bad apples" is difficult, however. "It depends on which day of the week you are counting," as one industry representative put it. There has been very little counting to date. No one even knows with precision how many elevators there are, let alone when they were all built and what kind of equipment they currently use. Harder still is determining the relative cleanliness or safety levels of grain-handling facilities. No industry group investigates or collects information on explosions. NFPA collects statistics through newspaper clippings and voluntary reporting from the fire service, but this information is hardly comprehensive. A USDA task force concluded that the NFPA estimate of annual fires in grain elevators may understate the actual situation by a factor of five.[13]