Chapter Six
Capital and Labor in the Industrial Revolution
"These valleys," wrote a Nailsworth local historian in 1880, "were [once] the center of the West of England cloth trade . . . , but trade declined, workmen and their families were driven elsewhere, mills were closed, and the masters were finding their occupations gone."[1] Gloucester possessed a thriving woolen trade from the late twelfth century until the Industrial Revolution, but between 1750 and 1850, Yorkshire usurped its long-standing premier position.[2] The lower district, containing Uley, Dursley, and Wotton-under-Edge, fell into disarray by 1835, while the Stroud district declined more gradually between 1830 and 1880.[3]
The anomaly of a declining economy in the midst of the Industrial Revolution has long vexed economic historians. Since Lipson and Clapham wrote a generation ago, scholars have ascribed the cause of decline mainly to entrepreneurial failure by Gloucester clothiers.[4] This emphasis, however, has been misleading. Lower district clothiers, Yorkshire's main competitors in coarser cloths, failed because of technical constraints on their ability to supply markets, and not because of their refusal to cultivate demand. Stroud clothiers, although plagued by the same difficulties, persisted longer because of the uniqueness of their fine cloth specialties. Despite their privileged market position, they showed themselves willing and able to exploit "a field for adventure" overseas.
The distinctive pattern of Industrial Revolution in Gloucester was instead responsible for the failure of the woolen trade. First,
the business cycle contributed to the growth of large-scale production units, which proved unviable in many cases. Second, capital formation in the adoption of new machinery followed classic patterns, but the use of steam power proved more problematic. Finally, the transition from cottage industry to the factory system profoundly altered the conditions of labor, but in a manner contributing to long-term economic decline.
The Course of the Business Cycle
Between 1800 and 1850, the most important trade depressions occurred in 1803/04, 1807/08, 1811, 1816, 1819, 1825/26, 1829, 1832, 1834, 1837-1842, and 1848/49.[5] The Napoleonic blockades caused the depressions of 1807/08 and 1811;[6] the collapse of demand following the end of the French Wars, and the fall in East India Company exports, following its loss of monopoly rights in India, precipitated the depressions of 1816 and 1819, respectively.[7]
The situation grew more complex after 1825 The crisis of 1826, the major divide of the era, began in the autumn of 1825, following the weaver strikes of the spring and summer, and the nationwide financial panic of November-December.[8] Economic stagnation continued in 1827 and 1828; although 1828 is thought to have marked an upturn in the trade cycle,[9] Mann conceded that the West already began feeling stiff competition from Yorkshire.[10] The Gloucester Journal noted only three bankruptcies, but four clothiers retired from trade, and seven others sold their mills.[11] The effects of the 1829 depression were still felt the following year. A partial revival had begun in the autumn of 1829, but the rate of profit remained low.[12] The year 1830 witnessed a large number of sales and leasing of mill property, and this trend continued into 1831. Thus, between 1825 and 1832, a pattern of continuous stagnation characterized developments in the cloth trade (see table 41).
Scholars have usually regarded the interval 1832-1836 as a period of prosperity.[13] In Gloucester, however, economic recovery was, in fact, precarious. The loss by the East India Company of its monopoly of the China trade in 1833 very likely contributed to the closing of those mills in the lower district specializing in lighter
TABLE 41. | ||||||||
Bankruptcy and sales by retirees from trade | Sales by nonbankrupts | |||||||
Year | Bankrupts | Decline in trade | Machinery and stock | Machinery at mill | Machinery and mill | Mills to | Mills for | Total |
1803/04 | 5 | 0 | 2 | 1 | 0 | 2 | 0 | 10 |
1805 | 7 | 2 | 0 | 0 | 0 | 0 | 2 | 11 |
1806 | 8 | 1 | 1 | 0 | 1 | 1 | 2 | 14 |
1807 | 3 | 0 | 2 | 0 | 0 | 1 | 1 | 7 |
1808 | 3 | 3 | 3 | 0 | 0 | 0 | 0 | 9 |
1809 | 2 | 0 | 2 | 0 | 0 | 1 | 2 | 7 |
1810 | 1 | 2 | 0 | 0 | 0 | 0 | 1 | 4 |
1811 | 3 | 1 | 1 | 0 | 0 | 0 | 2 | 7 |
1812 | 2 | 0 | 1 | 0 | 0 | 1 | 5 | 9 |
1813 | 2 | 1 | 0 | 0 | 1 | 1 | 1 | 6 |
1814 | 2 | 0 | 0 | 0 | 1 | 1 | 1 | 5 |
1815 | 6 | 0 | 0 | 0 | 0 | 0 | 1 | 7 |
1816 | 4 | 0 | 1 | 0 | 0 | 0 | 1 | 6 |
1817 | 3 | 2 | 1 | 0 | 0 | 2 | 2 | 10 |
1818 | 1 | 0 | 0 | 0 | 1 | 0 | 1 | 3 |
1819 | 4 | 1 | 2 | 1 | 0 | 1 | 1 | 10 |
1820 | 2 | 5 | 0 | 0 | 0 | 2 | 3 | 12 |
1821 | 7 | 2 | 0 | 0 | 1 | 0 | 1 | 11 |
1822 | 1 | 1 | 0 | 0 | 1 | 2 | 0 | 5 |
1823 | 2 | 0 | 0 | 0 | 1 | 0 | 1 | 4 |
1824 | 2 | 0 | 0 | 1 | 0 | 1 | 4 | 8 |
(Table continued on next page)
(Table continued from previous page)
Bankruptcy and sales by retirees from trade | Sales by nonbankrupts | |||||||
Year | Bankrupts | Decline in trade | Machinery and stock | Machinery at mill | Machinery and mill | Mills to | Mills for | Total |
1825 | 4 | 1 | 0 | 2 | 1 | 1 | 3 | 12 |
1826 | 7 | 0 | 1 | 0 | 0 | 0 | 1 | 9 |
1827 | 3 | 3 | 0 | 0 | 1 | 0 | 0 | 7 |
1828 | 3 | 4 | 1 | 0 | 1 | 1 | 6 | 16 |
1829 | 2 | 1 | 2 | 1 | 1 | 2 | 1 | 10 |
1830 | 1 | 3 | 2 | 2 | 2 | 5 | 6 | 21 |
1831 | 4 | 0 | 0 | 0 | 0 | 2 | 5 | 11 |
1832 | 3 | 0 | 0 | 2 | 0 | 0 | 0 | 5 |
1833 | 0 | 0 | 0 | 0 | 0 | 3 | 3 | 6 |
1834 | 1 | 2 | 0 | 1 | 0 | 0 | 1 | 5 |
1835 | 4 | 3 | 1 | 0 | 0 | 2 | 3 | 13 |
1836 | 0 | 1 | 1 | 1 | 1 | 1 | 5 | 10 |
1837 | 2 | 2 | 2 | 0 | 1 | 3 | 3 | 13 |
1838 | 2 | 1 | 0 | 1 | 0 | 1 | 0 | 5 |
1839 | 2 | 2 | 0 | 0 | 0 | 3 | 5 | 12 |
Source: Gloucester Journal ; see text. |
cassimeres and stripes.[14] Producers of superfines at Stroud, however, were reported doing a brisk business, despite the high price of wool: "Black superfines may be called the staple made of this borough," the Gloucester Journal reported, "and of those, well made . . . goods meet a ready sale.[15] Stroud clothiers, moreover, showed themselves sufficiently enterprising to fill the void in coarser lines left by the East India Company, despite Yorkshire competition. "[B]esides [the sale of Black superfines], it is surprising the quantity of cloths now making for the China market."[16]
This trend did not continue. The high price of wool soon produced "an extreme flatness" in the trade, which by March 1834 had existed "for the last four months." Yet employment was not too badly affected, since "the fine makers are working their old stock of wool into the market." Still, forecasts remained gloomy: "This Summer will be one of the worst for dearth of employment we ever had," because of the scarcity of foreign orders and saturation of the home market.[17] By July 1834 the Gloucester Journal could report "the still improving state of the fine cloth market."[18] By October, however, the full force of the crisis finally materialized: "Trade is dull and most transactions are done at a loss. Wool, though rather lower, continues . . . firm, but the manufacturers refuse to give the prices asked."[19] A month later, the failure of three London houses connected with the wool trade compounded the general apprehension.[20] Yet, by the end of 1835 a notable improvement had set in, which very likely continued into 1836.[21]
The years 1832-1836 witnessed the triumph of fine-cloth manufacturing as the principal staple of the Gloucester trade, with the industry now concentrated around Nailsworth and Stroud.[22] At the same time, uneven and precarious recovery, rather than unrelieved prosperity, characterized the period. Although the depression of 1834 may have been comparatively minor, it nevertheless produced a corrosive effect. Mere anticipation of its arrival contributed to a general atmosphere of insecurity, which partial economic revival in 1833 and 1835/36 failed to offset.
The depression of 1837-1842 gave the coup de grace in the short term to any hope of continuous prosperity. The severity of its impact demographically has already been noted for the Horsley-Nailsworth area.[23] The depression proved especially dev-
TABLE 42. | ||||||
Mills working | Rental value (£ ) | |||||
District | 1831 | 1841 | Mills void | 1831 | 1841 | Loss of |
Chalford, Painswick, Stroud | 100 | 63 | 37 | 22,919 | 9,480 | 13,439 |
Uley | 5 | 1 | 4 | 2,970 | 70 | 2,900 |
Wotton | 20 | 11 | 9 | 3,600 | 1,045 | 2,555 |
Dursley | 8 | 2 | 6 | 1,600 | 310 | 1,290 |
130 | 77 | 56 | 31,089 | 10,905 | 20,184 | |
Source: Gloucester Journal , 15 January, 1842. |
asting to the lower district. At Uley, 1,000 people reportedly emigrated,[24] and the value of mill property plunged drastically. A group of mills at Kingswood, which rented for £500 in 1814, carried an annual rental value in 1839 of only £100.[25] A dramatic shrinkage in the number of firms throughout Gloucester, but especially in the lower district, had accompanied this fall in value. Samuel S. Marling, a leading Stroud clothier, analyzed the condition of the Gloucester trade at a Bath anti-Corn Law meeting in 1842. His evidence, reproduced in table 42, illustrates the Stroud region's preponderance over the decade 1831-1841; the fall in number and value of Stroud mills, although considerable, was far smaller than at the lower district, an area already in decline by 1831.
At Stroud, a general economic revival took place toward the end of 1842 that lasted to the end of the decade and was led by super-fines producers, who busied themselves plying the China market.[26] The few who remained in business after 1850 concentrated on producing superfines until the last quarter of the century, when Stroud followed the lower district into decay.[27]
The business cycle often increased the incidence of bankruptcy over the 1800-1842 period and hence contributed to the decay of Gloucester's woolen trade. The trend in the turnover of firms
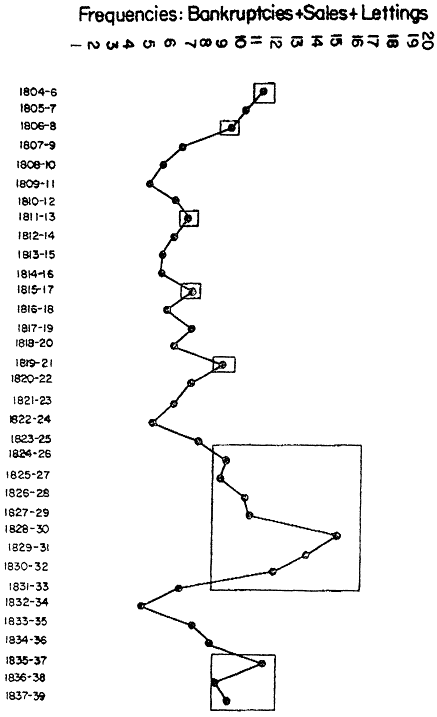
Fig. 17.
Three-year moving averages of business turnover, 1804-1839.
has been constructed from bankruptcy notices and sales advertisements placed in the Gloucester Journal and is illustrated in figure 17.[28] The squares plotted around particular averages or groups of averages indicate where a trough probably affected turnover significantly, or where an annual recession coalesced with a protracted period of stagnation.[29] The business cycle over this period helped to eclipse the small clothier and led to a concentration of ownership in larger, more heavily capitalized firms, many of which subsequently failed.
Construction of large-scale cloth mills began in the 1790s. Until 1826 the mills engaged principally in the preparatory processes of carding and scribbling, spinning, and the finishing processes of fulling, dyeing, and shearing. The early stages of the Industrial Revolution, moreover, took place in these particular branches of production.[30] Only rarely did the mills contain weaving sheds. Until 1826, weaving remained largely a traditional craft, undertaken by master artisans who employed journeymen and apprentices on a small scale.[31]
Many of these mills grew impressively large. In 1812 the five-story main building of Stonehouse Mills measured 70 feet long by 23 feet wide at its narrowest end, and it encircled an area upward of 2,000 square feet on each floor.[32] The premises contained jenny shops 170 feet long by 18 feet wide that held over eighteen spinning jennies of eighty spindles each, as well as weaving sheds and a dye house of comparable dimensions. New Mills, at Kingswood, considered "one of the largest and most powerful watermills in the West of England" in 1829, measured 150 feet long by 30 feet wide and was six stories high; five waterwheels on a high fall of 20 feet powered the mill.[33] An unnamed three-story cloth mill in the same vicinity stood 137 feet long by 31 feet wide and was powered by three waterwheels and a 20-horsepower Boulton and Watt steam engine. Its combined use of both energy sources produced a considerable sixty ends of cloth per week.[34] Uley Mills, when sold in 1837, belonged to Edward Sheppard, the largest clothier of the lower district. A combination of water and steam, with engines of 40-, 28-, and 20-horsepower, drove the entire complex and produced 100 ends of cloth per week.[35] Uley Mills contained, among a mass of ancillary items, thirty-nine scribbling and carding engines, fifteen spinning mules with 100 to 200 spindles each, and fourteen spinning jennies.[36]
Amid these large mills, many small clothiers could be found before 1825. Instead of occupying mills, they usually conducted their trade from workshops adjoining their homes. Cottagers undertook spinning and weaving for them, and fullers and dyers often performed the finishing work. In 1820 the occupier of Froome Hall Mills, for instance, advertised his services of slubbing, shearing, milling, and roughing to any clothier wishing to hire them.[37]
The inventory of the establishment of J. B. Hill, sold in 1813, typifies the style of the wealthier small clothier. His home and business included two parlors, four bedrooms, three attics, a brew-house, and workshops, which produced ten to fourteen ends of broadcloth per week.[38] "The House," noted its sales advertisement, "has been in the country trade for some years and if [a buyer] wishes to extend the business, he can get any quantity of wool spun into yarn in the neighborhood."
Smaller, less substantial clothiers usually held more than one occupation. William Keene was a clothier and cordwainer; John Harmer, a clothier and shopkeeper; and Richard Aldridge, a clothier and victualler.[39] However, a shopkeeper operating as a clothier might still have done so on a respectable scale. William Nichols possessed a stock in trade that included some of the most up-to-date machinery of the day: five 70-, one 50-, and two 40-spindle jennies; one 40-spindle billie; and two scribbling engines of 28 and 24 inches in length, all of which were powered by a horsewheel.[40] Small clothiers often relied on horsepower, and horsewheels were notable among clothiers' effects in early Gloucester Journal advertisements.[41]
The emergence of large mills, however, helped to drive smaller clothiers out of business. James Hubbard, a druggist at Nails-worth, recalled in 1838 that "formerly . . . there were from 40 to 50 [small clothiers] in the neighbourhood; but the operations of the larger manufacturers, when trade became limited, has swept them away."[42] Hubbard's observation can be supported quantitatively from the sales advertisements of mills, machinery, and stock that appeared in the Gloucester Journal .[43]
Table 43 groups these references into four main categories and breaks them down by several time intervals.[44] The findings indi-
TABLE 43. | ||||||
1804-1810 | 1811-1817 | 1818-1825 | 1826-1832 | 1833-1839 | Total | |
Machinery and stock | 21 | 5 | 5 | 7 | 3 | 41 |
Machinery at mill | 4 | 4 | 10 | 12 | 12 | 42 |
Mills to let | 6 | 7 | 6 | 8 | 13 | 40 |
Mills and machinery, and mills for sale | 8 | 17 | 31 | 44 | 31 | 131 |
Total | 39 | 33 | 52 | 71 | 59 | 254 |
Note: x2 = 57.05; df = 12; significance at 0.001: x2> 32.909. |
cate that a dramatic change in sales patterns took place.[45] A much larger than expected number of sales of small-clothier property transpired between 1804 and 1810 and remained consistently smaller than expected throughout the later periods. Mill sales by larger clothiers followed a reverse pattern. Actual sales were much smaller than expected in the 1804-1810 interval and much larger than expected between 1826 and 1832. Small clothiers failed in significant numbers early in the period, while the reverse was true of large clothiers. By the 1830s, the preponderance of large-clothier property in sales notices shows how far their mills had come to dominate the industry.
Between 1825 and 1835, moreover, these clothiers expanded mill premises to include weaving shops, made greater use of steam power, and began to replace the spinning jenny with the mule.[46] Indeed, this pattern of modernization refutes the argument of entrepreneurial failure often used to explain Gloucester's economic decline and for this reason merits closer scrutiny.
Capital Formation
Sales advertisements for the Gloucester Journal have made possible the documentation of capital formation processes in Stroud, Nailsworth, and the lower district. The mills appearing in these advertisements were each sold at various intervals, so that the tim-
ing of changes in the composition of capital can be easily located. These changes, moreover, clearly typified the capital formation processes occurring throughout Gloucestershire.
In 1805, Lightpill Mill, near the town of Stroud, housed five scribbling and carding engines, four shearing machines, and a gig mill.[47] The late occupant's effects contained neither jennies nor billies, suggesting that cottagers still performed the task of spinning. By 1824, no change had occurred.[48] Five years later, however, fourteen new scribbling and carding engines, all in their first cards, were put up for sale, together with twelve 80-spindle jennies, eight 60- to 70-spindle billies, seven cloth cutters, and eighteen shearing frames. The appearance of the jennies and billies indicated that spinning had been incorporated into the mill work, and the larger number of cutters, shearing frames, and engines pointed to significant growth in productive capacity. A 12-horsepower Boulton and Watt steam engine, moreover, had been added to the inventory.[49] By 1836, the mill worked sixteen engines instead of fourteen; a cloth steaming apparatus to render wool more malleable had been added; and a new 14- to 20-horsepower steam engine had replaced the older model. The mill was now capable of producing thirty ends of cloth per week.[50]
Fixed capital formation at Lodgemore Mills, also near Stroud, occurred even more dramatically, since the occupier, N. S. Marl-ing, had constructed many of its extensive buildings between 1824 and 1831[51] Lodgemore, one of "the most capable and desireable clothing establishments in the West of England," relied heavily on steam power, and with the use of water power produced an optimum 100 ends of cloth per week.[52] Similar developments took place at Nailsworth. In 1813 Dyehouse Mills housed "several [carding and scribbling] engines" in a loft and "newly erected machinery mill."[53] The advertisement did not mention jennies or billies, which meant that cottage spinners were still being employed. A mill located "at a convenient distance," moreover, undertook the fulling work. By 1828, Dyehouse Mills had been transformed into a complete factory. Its machinery included broad and narrow looms, housed in its weaving shops, with a 100-spindle mule for spinning.[54] A 14-horsepower steam engine complemented the use of water in powering the mill site.
At Inchbrook Mill, in Nailsworth, only two scribbling and card-
ing engines, two jennies, and one billy were being employed in 1820.[55] By 1832, its occupier had added a 200-spindle mule and introduced an 8-horsepower steam engine to complement the supply of water.[56] Three years later five scribbling and carding engines and two 200-spindle mules were in operation.[57] Following its sale in 1835, Inchbrook Mill passed to the ownership of Playne and Smith, clothiers from neighboring Dunkirk Mills.[58] Playne and Smith also ran Egypt and Hope Mills,[59] the previous tenants of which either succumbed to bankruptcy[60] or retired from trade.[61]
The type of large mill found at Stroud in the post-1825 period was more commonplace at Uley, Dursley, and Wotton-under-Edge in the early 1820s.[62] Stroud's fine-cloth specialties, with which Yorkshire could not compete and for which markets were relatively inelastic, brought less pressure on the region to innovate, although it did so in any case. The lower district's concentration on coarser cloths brought direct competition from Yorkshire, however, thereby forcing the region to develop more rapidly.
Hillsely Mill at Hawkesbury, near Wotton, had been used as a grist will in 1805. By 1821, however, it had become "a capital clothing mill with a steam engine of 25 horsepower, [able to drive] the whole of the machinery during a scarcity of water." At Kings-wood, one mile from Wotton, "a most complete and newly erected clothing manufactory, capable of making 40 ends per week," and containing two gig mills, six rooms for machinery, and a steam engine, was put up for sale in 1819. At Uley in 1823, a clothing factory was sold that produced forty-five to fifty ends per week and was powered by a strong stream and two 8-horsepower steam engines. At Dursely in 1824, an almost identical mill was put up for sale; it, too, produced forty-five to fifty ends per week and was powered by a well-running stream and two steam engines of 8- and 10-horsepower. Finally, a cloth factory at Cam, built in 1822 and sold three years later, utilized a 20-horsepower steam engine.[63]
Gloucester had clearly adopted on a wide scale all the machinery associated with the Industrial Revolution and, with the partial exception of the steam engine,[64] broadly kept pace with Yorkshire in this enterprise. By 1815 spinning jennies were appearing regularly in Gloucester Journal advertisements as part of the stock-
in trade of mill owners and occupiers.[65] According to Mann, the jenny and slubbing billy had been successfully introduced into the West of England after 1785, while the use of the mule first appeared in 1828 and spread rapidly after the strikes of 1829.[66] However, the sales of two mules in 1828 indicate that this type of machine must have been introduced earlier, since a lag very likely existed between the purchase and resale of each item.[67] In 1818 broad and narrow looms began to appear in the sales of ordinary mills,[68] although in small quantities and only intermittently until 1827.[69] Both the number of looms and the frequency with which they appeared in advertisements increased after 1826, and from 1830 they became permanent features of these notices.[70] According to the master weavers, "loom factories" in 1827 could house at a conservative estimate about 4,000 such devices.[71]
Although the timing of change differed between districts, the Gloucester woolen trade had clearly industrialized. The Industrial Revolution and the impact of the trade cycle permitted capital to concentrate in fewer firms, a trend that persisted at Stroud after the collapse of the lower district. Before 1826, capital concentration occurred because competition from newly capitalized mills gradually eliminated the small clothier. In this phase, the degree of concentration was really more relative, since the number of mill occupiers probably increased during the 1815-1825 period.[72] After 1826, when trade entered a critical period of stagnation, capital concentration assumed an absolute form, as successful clothiers acquired vacated mills.
The history of the Playne family firm vividly illustrates this tendency. In 1824 the prosperity that the family had experienced since 1795 led to the division of family assets between the brothers William and Peter and the subsequent creation of two firms. William remained at Longfords Mill, and Peter established his firm at Dunkirk.[73] Eventually, as we have seen, Peter's firm acquired Inchbrook, Hope, and Egypt Mills and benefited from capital-generating processes undertaken by its predecessors.[74] It was also true that successful clothiers, by virtue of capital accumulated elsewhere, frequently modernized the mills they occupied as leasehold property. N. S. Marling undertook the modernization of Lodge-more Mills during a seven-year period of his tenancy;[75] he belonged to a substantial clothier family and had previously occu-
pied other mills in the Stroud region.[76] If the Gloucester woolen trade had therefore successfully industrialized, why did "deindustrialization" occur and virtually at the same moment? The answer hinges on the extent and nature of Gloucester's employment of steam power.
Yorkshire clothiers adopted steam power sooner than did Gloucester clothiers, and scholars have generally agreed that earlier innovation in this area gave the North a critical advantage.[77] Yorkshire clothiers benefited from significantly lower coal and transport costs, which encouraged them to innovate,[78] and in 1800 they employed nearly eighty steam engines. According to Mann, Gloucester clothiers began to adopt steam power gradually from 1819 but not on a sufficiently wide scale until 1829, when the gap between counties seems to have widened appreciably.[79]
This interpretation, however, contains several defects. When comparing Gloucester to Yorkshire, one must first distinguish between Yorkshire's principal subregions. Most of the early Yorkshire steam engines were concentrated in the East Riding, around Leeds and Bradford, where the water supply was less satisfactory, rather than at Huddersfield and Saddleworth in the West.[80] West Riding clothiers, according to Gregory, "had started to take more interest" in steam engines around 1800; but the division between East and West Riding persisted as late as 1835 and began to narrow only in the following three years.[81] West Riding seems to have occupied an intermediary position between Gloucester and the East Riding; a comparison between Gloucester and the West Riding, therefore, seems more appropriate than the county by county analyses undertaken by both Gregory and Mann.
Furthermore, comparisons between Gloucester and Yorkshire with respect to the adoption of steam power have usually based themselves erroneously on an 1838 parliamentary return.[82] In order to explain Gloucester's lack of competitiveness, Mann has shown that its mills relied more heavily on water than on steam, and Gregory has demonstrated that the aggregate capacity of Gloucester steam engines in 1838 fell considerably below Yorkshire's.[83] However, the return does not register the true extent of Gloucester's reliance on steam power over the entire course of the Industrial Revolution nor gives a clear indication of the timing of that county's economic decline.
Gloucester clothiers began adopting steam engines in more reasonable numbers and at higher capacity during the 1820s than Mann has implied,[84] and the economy of the lower district and much of Stroud's had already collapsed by 1838. Many mills that utilized steam had thus long ceased to operate.[85] The depression of 1829 was especially severe, and the number of working mills at the lower district was already low by 1831.[86] Any comparison between Gloucester and Yorkshire and 1838 must therefore adjust for the far fewer number of Gloucester mills remaining in operation and must not accept the level of its aggregate steam-power capacity at face value. The smallness of this capacity at this time was the result, not the cause, of economic decline.
Tables 44 and 45 summarize the power conditions of West Riding and Gloucester Mills in 1838. Although the West Riding clearly outstripped Gloucester in numbers of operational mills and in aggregate steam-power capacity, a per capita analysis reveals a less dichotomous relationship between the two regions. The West Riding surpassed Gloucester marginally in per capita steam power capacity, while Gloucester surpassed its rival more significantly in total per capita power because of heavier reliance on water. When improved carefully, however, water power easily matched the productivity increases effected by steam.[87] Gloucester's per capita power advantage in 1838 indicates the persistence of a competitive industry, regardless of the extent to which previous crises had reduced its size; it also suggests that the causes of industrial decline must be sought elsewhere, perhaps in the manner of innovation itself.
Gloucester clothiers used steam engines more regularly and at higher capacity than scholars have usually admitted. High coal and transport costs, combined with the cheapness of operating water, constrained Gloucester clothiers from substituting steam engines for water power. Still, the construction of mill ponds and waterwheels required more capital than that needed for investment in the equivalent amount of steam power.[88] For this reason, too, Gloucester clothiers shied away from complete substitution. When faced with the choice of upgrading existing water-power structures or supplanting them altogether with steam, clothiers often made the more rational decision to add a waterwheel or expand existing ponds and leets.[89] Otherwise, the capital costs of
TABLE 44. | |||||||||
Steam engines, waterwheels, and HP intervals | |||||||||
Region | Number of mills | 50 + | 40-49 | 30-39 | 20-29 | 10-19 | 0-10 | Total | |
West Riding | 600 | SE: | 13 | 21 | 74 | 87 | 138 | 44 | 377 |
SHP: | 790 | 855 | 2003 | 1931 | 1875 | 296 | 7750 | ||
WW: | 1 | 2 | 7 | 27 | 91 | 109 | 237 | ||
WHP: | 60 | 80 | 226 | 370 | 1114 | 593 | 2443 | ||
Gloucestershire | 96 | SE: | 1 | 3 | 6 | 8 | 22 | 9 | 49 |
SHP: | 50 | 125 | 157 | 171 | 287 | 53.5 | 843.5 | ||
WW: | 0 | 0 | 3 | 8 | 42 | 166 | 219 | ||
WHP: | 0 | 0 | 90 | 180 | 526 | 922.5 | 1718.5 | ||
Note : SE = number of steam engines; SHP = steam horsepower; WW = waterwheels; WHP = water horsepower. | |||||||||
Source: British Parliamentary Papers 1839, XLII, "Accounts and Papers," return of mills: Horner's and Saunder's districts for the West Riding, and Howell's district for Gloucestershire. |
TABLE 45. | ||||||||
Region | Number of mills | SE/M | SHP/M | SHP/E | WW/M | WHP/M | WHP/W | Total HP/M |
West Riding | 600 | 0.6 | 12.9 | 20.6 | 0.4 | 4.1 | 10.3 | 17.0 |
Gloucestershire | 96 | 0.5 | 8.8 | 17.2 | 2.3 | 17.9 | 7.8 | 26.7 |
Note : SE = number of steam engines; SHP = steam horsepower; WW = number of waterwheels; WHP = water horsepower; total HP = total horsepower;/M = per mill;/E = per engine;/W = per waterwheel. | ||||||||
Source: British Parliamentary Papers , 1839, XLII, "Accounts and Papers," return of mills: Horner's and Saunder's districts for the West Riding, and Howell's district for Gloucestershire. |
the original structures would burden profits,[90] while the costs of adding to them, if kept within strict limits, were probably lower than full-scale investment in steam. Nevertheless, clothiers sometimes purchased one or more steam engines instead and used them to supplement the flow of water. Steam engines clearly enhanced the productivity of water mills,[91] and by using them in this manner, Gloucester clothiers sought to extract the cost advantages offered by both energy sources while minimizing their disadvantages. The mixed use of steam and water, however, created problems of excess capacity, which rendered firms vulnerable to failure.
Although scholars have long recognized such usage, they have treated the relationship between the two energy sources dichotomously: Steam power served either as an adjunct to the water supply in emergency situations or as a complete substitute for it.[92] Gloucester clothiers actually combined both energy sources routinely on a year-round basis because of the endemic irregularity of the water supply.
Gloucester clothiers used steam power to increase output directly or indirectly. Sometimes they connected their engines directly to machinery and in this way ran entire buildings of a mill complex, while water operated others.[93] Otherwise steam engines were connected to the waterworks of a single mill and used to supplement a weak water flow or substitute for water entirely during dry seasons, or sometimes they served as pumps to facilitate the flow from lower to upper mill ponds.
By using steam engines in this manner clothiers might increase capital costs without increasing output to a compensating degree. Unit capital costs would thus remain high, and excess capacity would result. Excess capacity might occur if the amount of steam power employed was either too great or too small. A balance needed to be found, and this was something difficult to estimate.
Analysis of a sample of mixed powered mills, advertised for sale or rental in the Gloucester Journal by bankrupts, their assignees, or those retiring from trade, and reproduced in table 46, has shown the need to distinguish between mills using large engines and those using smaller engines.[94]
Large engine mills generated sufficient steam power to produce directly the higher levels of output noted in advertisements while
TABLE 46. | ||||||
Name of mill | Year | Ends per week | Steam | High-/ | Water | Total |
At Avening | 1825 | 35 | 32 | H | (31.3) | 63.3 |
Lightpill Mill | 1834-1836 | 30 | 17 | L | (20.7) | 37.7 |
A cloth mill | 1824 | 43 | 20 | H | (22.8) | 42.8 |
Cooke's Mill | 1824 | 20 | 10 | L | (15.7) | 25.7 |
Dyehouse Mills | 1828-1830 | 30 | 14 | L | (18.5) | 32.5 |
A newly built mill | 1821 | 30 | 14 | L | (18.5) | 32.5 |
A mill at Cam | 1825 | 60 | 20 | H | (22.8) | 42.8 |
Uley Mills | 1837 | 100 | 88 | H | (71.1) | 159.1 |
A mill at Uley | 1823 | 48 | 16 | L | (19.9) | 35.9 |
Avening Great Mill | 1833 | 30 | 28 | H | (28.5) | 56.5 |
Lodgemore Mills | 1832 | 100 | 40 | H | 30.0 | 70.0 |
A cloth mill | 1830 | 40 | 12 | L | (17.1) | 29.1 |
Hathaway's Mill | 1831 | (30.4) | 8 | L | (14.3) | 22.3 |
Hillsley Mill | 1821 | (46.6) | 25 | H | (26.3) | 51.3 |
Toghill's Mill | 1827 | (34.2) | 12 | L | (17.1) | 29.1 |
A fulling mill | 1821 | (34.2) | 12 | L | (17.1) | 29.1 |
Slad Mill | 1836 | (47.5) | 26 | H | (27.0) | 53.0 |
Rookhouse Mill | 1832 | (39.9) | 18 | L | (21.4) | 39.4 |
Seville's Mill | 1837 | (38.0) | 16 | L | (19.9) | 35.9 |
Woodchester Mill | 1839/40 | (51.3) | 30 | H | (29.9) | 59.9 |
At Woodchester | 1828 | (34.2) | 12 | L | (17.1) | 29.1 |
Peghouse Mill | 1830 | (31.4) | 30 | H | (29.9) | 59.9 |
Newcombe's Mill | 1839 | (34.2) | 12 | L | (17.1) | 29.1 |
Freame's Mill | 1827 | (30.4) | 8 | L | (14.3) | 22.3 |
Inchbrook Mill | 1832-1835 | (30.4) | 8 | L | (14.3) | 22.3 |
Harrison's Mill | 1829 | (34.2) | 12 | L | (17.1) | 29.1 |
Oldland's Mill | 1832 | (38.0) | 16 | L | (19.9) | 35.9 |
Dutton's Mill | 1835 | (34.2) | 12 | L | (17.1) | 29.1 |
Wallington's Mill | 1830 | (36.1) | 14 | L | (18.5) | 32.5 |
A cloth mill | 1830 | (70.4) | 50 | H | (44.1) | 94.1 |
A cloth mill | 1830 | (41.8) | 20 | H | (22.8) | 42.8 |
A cloth factory | 1830 | (36.1) | 14 | L | (18.5) | 32.5 |
Blue Mills | 1828 | (32.9) | 10 | L | (16.7) | 26.7 |
Merritt's Mill | 1839 | (41.8) | 20 | H | (22.8) | 42.8 |
Note : The figures in parentheses were arrived at through linear estimators; see Urdank, "Economic Decline," p. 431, n. 21. A detailed catalog of Gloucester Journal advertisements for the sale of cloth mills has been assembled in Urdank, "Dissenting Community," appendix 5.1. |
compensating simultaneously for the irregularity of the water flow. Although the water supply, when enhanced by steam, contributed to greater output, the full thrust of steam's indirect effect necessarily became attenuated,[95] and productivity advances remained moderate. Had large engine users relied solely on the direct effect of steam, productivity would have been much greater, or less steam power would have been needed to achieve the higher levels of output advertised.
Small-engine mills, in contrast, generated insufficient steam power to produce directly the levels of output advertised. Half of the capacity of steam was directed toward output, while the other half compensated for the irregularity of the water supply. Neither effect, however, was very significant. Small-engine users enjoyed comparatively better water flows and must have thought their mills required less steam power to compensate for the irregularity in the water supply. Unfortunately, they underestimated the amount of steam power needed. Productivity advances thus remained minimal, and unit capital costs undoubtedly rose, thereby contributing to failure.
In general, large-engine mills employed too much steam power, relative to output levels, while small-engine mills employed too little. For these diametrically opposite reasons, both types of mill suffered fatally from excess capacity.
Capital formation, whatever its degree of success, affected the conditions of labor. In the long term, excess capacity, by promoting bankruptcy and retirements, led to the decay of the woolen trade and consequently to the loss of employment. The rhythm of the business cycle encouraged capital concentration, but employment opportunities actually declined, although the volume of production continued its steady advance.[96]
The adoption of machinery inadvertently led to structural unemployment by replacing labor in the productive process. A. R. Fewster accurately predicted that handloom weavers would follow the paths of scribblers and shearmen,[97] and Peter Playne opined that the weavers were "racing against steam." "The slightest rise for wages," Playne maintained, "would cause [the] general adoption of power-[looms] throughout the country."[98] It was a race his own weavers lost.[99] Factory organization had created a surplus weaver population even prior to the advent of powerlooms;[100]
moreover, as the mule, with far greater number of spindles,[101] superseded the jenny, spinners began to suffer the same condition.
In the short term, however, the impact of capital formation on labor was more complex. Did factory labor represent an improvement over the conditions of cottage industry? From the manufacturer's standpoint it certainly did, since by acquiring complete control over the instruments of production, he could establish his own regime of work discipline. For labor, however, the answer was less simple. Although custom-minded weavers may have protested against factory life, changes in the sexual division of labor, labor productivity, and earnings produced mixed results.
Capital and Labor
Under the system of protoindustrialization, or cottage industry, the family often served as the primary unit of production, with all members contributing their earnings to its common budget. "In the weaver's household," Scott and Tilly have written, "children did carding and combing, older daughters and wives spun, while the father wove."[102] Yet customary practices persisted longer than this characterization suggests; master weavers often rented or purchased workshops to house the looms used by their journeymen, who necessarily worked away from their homes.
Although the size of the weaver population of the early nineteenth century is difficult to estimate, a Horsley census of householders for 1811 offers some idea of its importance.[103] The list records the tenurial status of the household head as a tenant or "landlord" and thus offers a measure of the likely proportion of extant master weavers, since the prosperous ones among them probably owed rather than rented their workshops.[104] George Ford of Elcomb, Uley, in a typical example, put up two lots for sale in 1817 that he described as "desireably situated for a weaver"; they included "a new-built messuage . . . with broad and narrow loom shops [and] a new-built tenement adjoining the above," which presumably served as a dwelling.[105]
Table 47 presents a breakdown of landlords and tenants by occupation, mean household size, percentage of respective occupational group, and percentage of all listed householders.[106] The findings show that weavers accounted for nearly 30 percent of all Horsley householders, a significantly higher percentage than
TABLE 47. | |||||
Occupation and tenurial status | N | Percent of all occupants | Percent of all household heads | Mean number of household heads | Coefficient of variation |
Craftsmen all | 92a | 100 | 15.9 | 4.88 | 48.2 |
Craftsmen landlord | 31 | 33.7 | 5.2 | 4.65 | 54.0 |
Craftsmen tenant | 58 | 63.0 | 9.7 | 4.74 | 46.2 |
Weavers all | 176b | 100 | 29.6 | 5.06 | 46.6 |
Weavers landlord | 47 | 26.7 | 7.9 | 5.19 | 51.6 |
Weavers tenant | 114 | 64.8 | 19.2 | 4.96 | 45.6 |
Laborers allc | 99 | 100 | 16.6 | 5.01 | 45.1 |
Laborers landlord | 14 | 14.1 | 2.3 | 5.50 | 43.8 |
Laborers tenant | 85 | 85.9 | 14.3 | 4.98 | 46.8 |
Note : The total number of household heads contained in the census listing equals 595; the total number in this table constitutes 62 percent of the whole. The table does not include several social groups, such as gentlemen, yeomen, widows, clothiers, or small shopkeepers, who are listed in the census but whose presence does not touch the point being analyzed. | |||||
a Craftsmen included masons, tailors, carpenters, cordwainers, glaziers, sawyers, pargeters, plasterers, saddlers, shearmen, wheelwrights, millwrights chairmakers and blacksmiths. Three had no discernable tenurial status. | |||||
b Fifteen weavers were listed as nonresidents, and while included in the total, were excluded from analysis by tenurial status. All were tenants, but since they were nonresidents, they were probably also master weavers who had rented working premises. | |||||
c The census listing drew no distinction between agricultural laborers and day laborers associated with the cloth trade. |
craftsmen or laborers. Weavers, moreover, were as likely to have been landlords as their fellows in other crafts,[107] and as might have been expected, landlord-laborers represented a far smaller proportion of all laborers listed.[108] Clearly, large numbers of master weavers could be found in 1811, and they enjoyed a social status equal to that of other independent craftsmen.[109]
From 1800, however, the independent status of master weavers
TABLE 48. | |||||
1811 | 1841 | ||||
Occupation | N | % | N | % | % change |
Weavers | 176 | 29.6 | 101 | 15.4 | -42.6 |
Spinners | 21 | 3.5 | 14 | 2.1 | -33.3 |
Shearers | 21 | 3.5 | 0 | — | - 100.0 |
Clothworkers | 7 | 1.2 | 47 | 7.2 | +571.4 |
Subtotal | 225 | 37.8 | 162 | 26.2 | -28.0 |
Laborers | 99 | 16.6 | 191 | 29.2 | +92.9 |
Artisans | 92 | 15.5 | 99 | 15.1 | +7.6 |
Clothiers | 20 | 3.4 | 4 | 0.6 | -80.0 |
Total | 595a | 655 | |||
a See the general notation in table 47. | |||||
Sources : 1811 manuscript census (see n. 103 and text); 1841 census enumerators' lists (PRO Home Office 107/363). |
began to erode slowly. "Loom shops" first appeared in that year, and several years later Parliament repealed the Tudor Statutes, which had long protected the customary structure of the trade.[110] Still, between 1814 and 1825, master weavers believed strongly enough in the durability of their craft to have trained a surfeit of apprentices;[111] loom shops did not pose a serious threat to them until 1827.
The rise of capital-intensive factories by 1841 eliminated the master weaver's traditional status and reduced demand for skilled woolworkers generally. Table 48, based on comparative census data,[112] shows Horsley weavers having declined by 40 percent of all household heads between 1811 and 1814. Spinners, although initially small in number, fell by a third. Shearmen disappeared entirely, and unskilled clothworkers rose in number by more than 500 percent. Woolworkers as a group declined by 28 percent as the number of day laborers increased 93 percent, while the 80 percent fall in the number of clothiers suggests a growing concentration of capital.
Still, among journeymen outworkers, a family-centered approach
TABLE 49. | |
Occupation | Number |
Weavers | 59 |
Spinners | 13 |
Clothworkersa | 45 |
Laborers | 3 |
Seamstresses | 4 |
a Quillers, burlers, reelers, pickers, and warpers. | |
Source: British Parliamentary Papers ; see text. |
to work predominated during the era of protoindustrialization and remained intact in the first stages of transition to the factory system. Early factory masters permitted operatives to hire their wives (see table 49) and children as assistants and therefore used the family as an agency for labor recruitment.[113] "Sir, it is the parent who makes the contract, and who sanctions the work of the child," W. H. Hyett, M.P. for Stroud, remonstrated against the first factory act; "and I apprehend that the wisdom of Mr. Sadler . . . will have some difficulty in finding a stronger safeguard for the child, than the natural affection of the parent."[114]
This traditional system gradually deteriorated, as labor recruitment began to base itself more fully on the free market. The Gloucester weavers, who in 1827 complained of the rise of "loom factories," also directed their protest against its unsavory, residual consequences. Manufacturers, they asserted, began employing "strangers in those factories, from other counties . . . [who] not infrequently . . . became the fathers of illegitimate children."[115] By individualizing labor recruitment, the factory system thus eroded the primacy of the family as an economic unit and even threatened its social stability.[116]
A repatterning of the division of labor within the household began to occur. As men moved into the factories, women became increasingly confined to the domestic sphere, although some continued to work, however irregularly. Four of the largest mills in the Stroud, Eastington, and Nailsworth areas in 1839 employed a total of 195 male weavers, only three of whom were unmarried. Of the remaining number, about one-third of the wives had no
TABLE 50. | ||||
Occupation | Mean (s) | Standard deviation | Percent mean household- | Mean household- |
Weavers | 4.6 | 2.18 | 30.0 | 15.27 |
Spinners | 3.9 | 1.39 | 24.5 | 15.93 |
Clothworkers | 3.25 | 1.72 | 19.7 | 16.43 |
Source: British Parliamentary Papers ; see text. |
occupation, while the others were employed in various capacities in the cloth trade.[117] Where the wife did not work, the burden of supporting the household fell on the husband and the children; where she did work, her industrial labor very likely remained subordinated to her household duties.[118] The percentage distribution of mean earnings of wives who wove cloth, depicted in table 50,[119] reflected this tendency.
Although women weavers contributed nearly one third to the total household income, the mean of 4.6s (4s.7d) was far below what they would have earned as factory weavers but roughly equal to what they could be expected to have earned as cottagers.[120] Women, of course, worked in factories, but because of the persistence of the domestic system, albeit in a weakened form, they did not necessarily precede men, as they had in the cotton industry.[121] Nor were there as many female occupations. Of nineteen total available occupations, apart from weaving and jenny spinning, men occupied eleven, children three, and women five.[122] Weaving and spinning were mixed occupations, albeit male-dominated.
In the heyday of the domestic system, weaving had been strictly confined to males. Women may have assisted their journeymen husbands by taking a turn at the loom; or if they took up the trade more regularly, they did so indirectly through service in a household, since master weavers excluded them from apprenticeship. The Napoleonic wars altered this situation. The shortage of male labor, combined with the great demand for cloth, created opportunities for women to become weavers more formally.[123]
Nevertheless, weaving remained a predominantly male occupa-
tion. At Horsley parish in 1811, while the ratio of female householders to all household heads was 99:526, or 18.6 percent, the ratio of women weavers, listed as householders, to all weaver householders was only 7:195, or 3.6 percent.[124] As the domestic system came into competition with the factory, more women entered the trade, but mainly as outdoor weavers. By 1841, at Horsley, their proportion had increased to about 36.0 percent of all weavers.[125] In a sample of forty Gloucester mills, however, they accounted for only 26.0 percent of all handloom weavers, representing a significantly lower proportion.[126]
The condition of female spinners altered more dramatically. Spinning had begun as a female occupation under the domestic system and remained so for some time after the introduction of the jenny. Hargreaves's original invention contained only eight spindles, but by 1810 the jenny could accommodate sixty, seventy, and eighty spindles.[127] Although contemporaries, as late as 1838, still regarded jenny spinning as a female occupation, males had begun encroaching on this preserve as early as 1811.[128] With the increase in spindle capacity, the operation of jennies required greater physical strength; large jennies were routinely employed in mills and those with seventy and eighty spindles, at the very least, were probably male-operated. When manufacturers adopted the mule in the late 1820s, it displaced jenny spinning by about 60.0 percent.[129] Mules, with 100 to 200 spindles, required male labor even more than did larger jennies, especially after employers began arranging them in facing pairs, so that one spinner might operate two machines.[130] If males became mule spinners, working regularly in factories, then women remained at the jenny, laboring irregularly at home amid their domestic duties.[131] The Industrial Revolution greatly transformed spinning and weaving. Unlike scribblers, carders, and shearmen, who were entirely displaced by innovation, spinners and weavers became bound more closely to the rhythm of machinery. Spinners were forced to master rising spindle capacities with speeds of up to 6,000 revolutions per minute; experienced spinners averaged three and one half draws per minute over a fifty-seven-hour week.[132] The progress of both jenny and mule spinning resulted in the production of finer yarns, which, with other changes in weaving, greatly affected weaver productivity.
The fly shuttle, widely adopted in Gloucester by 1798, enhanced weaver productivity by shortening the average labor time between a quarter and a third.[133] Where once two weavers had been required to operate a loom, one working the warp and the other the weft, the fly shuttle enabled one weaver to perform both operations.[134] In 1824 manufacturers altered a customary work rule by lengthening the warping bar from 16-hundreds to 20-hundreds while increasing the number of shoots per yard in the weft.[135] Because of the use of finer yarns, this innovation produced a denser fabric.[136] "[O]f late years," the weavers complained, "the work has been drawn so small that it requires a great deal of time and attention to do justice to the manufacturer."[137] Indeed, the combination of all these changes, compounded by the discipline of the factory, greatly intensified the weaving process.[138]
This intensification affected men and women differently, since males eventually came to dominate both spinning and weaving. Where it is possible to compare the productivity of the sexes, we find males adapting more completely to the new structure of work. Male factory weaver productivity in 1838, for instance, stood at 1,044 yards per weaver per annum, while female factory weavers produced at a significantly lower rate of 930 yards per weaver per annum.[139] For this reason, some manufacturers preferred to employ male weavers and sought to legitimate paying females at a lower rate, as master weavers had done in an earlier period. "Women are not so regular in their time as men," Peter Playne contended, "nor so able to perform the work in the same time. Thirty men will do as much work as forty women, and the outlay for looms, buildings, etc., is greater for a number of females than for male weavers."[140] The altered structure of work affected semi-skilled labor, such as warping or piecing, according to the degree of its synchronization with a skilled occupation.[141]
A comparison of factory weaver productivity with that of the outdoor weaver best illustrates the effect of the new structure of work on the labor process. Factory weavers produced 1,974 yards per weaver per annum, while outdoor weavers produced only 701.7 yards per weaver per annum.[142] Preindustrial journeymen weavers worked as long as necessary to earn their customary wage. This meant that they worked seriously only three to four days of every week.[143] Changes in the structure of work, which
foreshadowed the factory system, gradually subjected them to a more rigorous regime. Under the factory system, where the clothier governed the conditions of labor, however, former journeymen worked longer and more regularly than possible under the master weaver's direction.[144]
This change produced both positive and negative consequences· On one hand, the acceleration and increased laboriousness of weaving clearly made work more stressful, although far less so than in the Lancashire cotton industry.[145] On the other hand, factory discipline imparted a new sense of order, which made weavers more self-possessed. "The factory system," one employer remarked, "decidedly tends to improve the men, to break through the sluggish habits for which weavers have been so notorious; it tends to make the men at once punctual and industrious."[146] By doing so, the factory enhanced their capacity for self-organization, expressed collectively through a trade union, or by individual initiative in pursuit of higher earnings. Evidence given by the weaver Thomas Cole illuminates this point especially well:
In the factories more work is done, as the men are evaluating each other. . . . Looms are in much better order in the shop factories than they were at the houses of weavers; people . . . had not the notion of putting them in order; a man can earn more now at a loom . . . from improvements in the tackle. . . . [T]he men do earn more money than they could out; in short they settle their minds to work . . .; they did not used to be so active in the master's houses; they often would get out of the loom and daudle their time, and have a drop of beer, etc. Thinks the factory system has given the men more settled habits, and there is not so much time spent in the public houses as used to be. Has heard many shopweavers say that if the wages were a little higher, they would be much more content to work in a factory than out of it; has heard many of the men who work for Mr. Playne say so; Isaac Kaynton and Joseph Cole, my son, are of the same opinion.[147]
Thomas Cole's belief in the superiority of the factory system was a mark of deference, conditioned by a teetotalist, Nonconformist sensibility; it displayed an identification with his employer's view on the issue of worker control that most weavers believed contrary to their interests.[148] Once a master weaver, Cole relinquished his independence with almost casual equanimity: "was formerly a master weaver, and kept two looms, but went into the
factory because his employer put out little work."[149] Apparently, no resentment lurked behind his decision to have done so. Nonetheless, this pattern of deference was paradoxical because it stemmed from the memory of his earlier, independent position. His assessment of the work habits of journeymen weavers was based on his experience as their former employer, and on this basis it displayed an unwitting empathy with the clothier.[150] Thomas Cole, in other words, accepted in principle the clothier's claim of authority over his weavers, because he had once exercised the same power as a master in his own house.[151]
Such agreeability, however, could dissipate under altered circumstances. Festering grievances could easily subvert a deferential temperment informed by individualism. Because he had been a master weaver, Thomas Cole was also sensitive to injustice at the workplace, a sensibility partially informed by a Nonconformist conscience. Under proper conditions, he might even have emerged as a strike leader, despite admonitions from his chapel's deacons.
Cole had been baptized at Shortwood in 1806 and excluded from membership in 1834.[152] Although the church roll did not state the reason for his exclusion, circumstantial evidence suggests that it may have been the strike against William Playne at Long-fords Mill that same year.[153] Baptists were known for excluding members who engaged in strikes, and the Shortwood deacons, in particular, explicitly lamented their members' attraction to trade unionism.[154] Cole was not completely uncritical of the factory system: "[Its] greatest injury, witness thinks, . . . is the walking to and from the shop."[155] He was clearly dissatisfied with the wages paid by Mr. Playne; his delicate reference to that manufacturer in the context of his general approval of factory earnings must be understood as a veiled criticism. It may have been possible to earn more as a factory weaver, because of better looms and the faster pace of work, but manufacturers often used this fact to legitimate paying lower piece rates; between 1825 and 1838, wages underwent a great fall.[156] Cole admitted, moreover, that he no longer worked as a factory weaver "in consequence of some strife with the foreman."[157]
The great majority of factory weavers did not share Cole's generally favorable appreciation of the factory system, despite his assertion to the contrary In a survey of over 190 weavers at four
TABLE 51. | |||
Former Status | |||
Condition | Master | Journeyman | Total |
Improved | 3 | 9 | 12 |
Not improved | 90 | 89 | 179 |
Total | 93 | 98 | 191 |
Source: British Parliamentary Papers ; see text. |
mills in Stroud and Nailsworth undertaken by a parliamentary commissioner, the respondents overwhelmingly rejected the proposition that their condition might have improved since entering the factory. Table 51 presents the joint distribution of their answers by their former status of master or journeyman.
These results are of special interest because factory weavers, on average, earned more than did outdoor weavers (approximate weekly earnings for factory weavers were 11s. 9d. per week; for outdoor master weavers, 8s. 1 ½ d.; outdoor journeyman weavers earned 6s. 10 ¼.).[158] Clearly, wages were not the sole criterion by which factory weavers measured their standard of living. Their distaste for working in a mill setting, rather than in intimate surroundings, and their chronic fatigue, caused by the need to walk to work, were more important considerations. Finally, most perceived factory work as less prestigious than craft labor. Master weavers forfeited their independence and could no longer entertain the ambition of becoming clothiers, while journeymen relinquished the hope of one day establishing their own shops (see data presented in table 52).[159]
Under the factory system, "training to the loom" could be undertaken without having to preserve the "mysteries of the craft." Youths, formerly trained as "colts" by master weavers,[160] could be given a fair chance to compete with their former employers, with output alone determining the level of their skill. Nevertheless, rewards were not always commensurate with effort
TABLE 52. | |||||
N | Average price | Average weekly earnings | Average chain length (hundreds in chain) | Average weaver timeb | |
Master | 93 | £1.15s. ![]() | 10s. 7d. | 17.58 | 17.5 |
Journeyman | 98 | £1.13s. ![]() | 10s. 7d. | 17.53 | 16.5 |
a t= 2.354, df = 193, t> 2.326 at 0.02 probability. | |||||
b t= 1.778, df = 190, t> 1.65 at 0.05 probability (one-tailed test); the two-tailed test, however, is not significant since t> 1.960 at 0.05 probability. | |||||
Source: British Parliamentary Papers ; see text. |
under the factory regime. Among the weavers surveyed, former masters on average were still paid a higher price per piece, although they were generally less efficient than former journeymen. All weavers wove the same average length of chain, but former journeymen tended to finish the piece one day sooner, and after deductions for defects in the finished product, their average weekly earnings equaled those of their former masters.[161] The fact that former journeymen worked faster, produced fewer defects, and yet were paid at a lower gross price per piece affirmed the weavers' suspicion that once the clothier knew their speed, he would try to lower their wages. They could draw little consolation from the fact that their wages were higher and employment more regular than those for outdoor weavers. Whereas the factory system may have enhanced productivity, the existence of an outdoor surplus weaving population paid at lower rates merely served to restrain the legitimate claims of factory weavers for even higher wage rates. Threats of dismissal and black-listing were also grizzly warnings to disaffected factory weavers, who unionized in spite of them.
Wages for all categories of workers, furthermore, were declining over the course of the thirty-year period prior to the parliamentary commissioner's inquiry. The negative consequences of this fall were apparent only from 1829, and became more pronounced after 1835. Wheat prices, depicted in figure 18, were falling at an average rate of 2.9 percent per annum, as a result of the
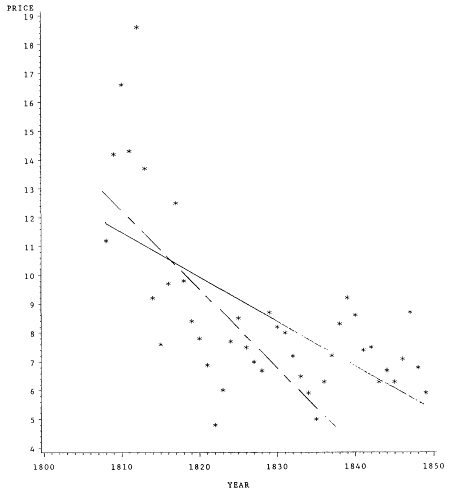
Fig. 18.
Gloucester Market Wheat Prices, 1808-1849.
Key: Solid Line (1808-49):Price = 11.7 - 0.15 (time)
Broken Line (1808-37): Price = 12.9 - 0.26 (time)
chronic agricultural depression of the postwar years.[162] The movement of wheat prices, of course, determined the fluctuations in the price of bread, which could account for as much as 45 percent of a weaver's budget.[163] A comparable annual wage series is not available, but one is extant for the period by yearly intervals, grouped according to when the actual fall in wages occurred. Table 53 pre-
TABLE 53. | |||||||
1808-1816 | 1817/18 | 1819-1828 | 1829-1835 | 1836 | 1837 | 1838 | |
Wheat | 13.17 | 10.66 | 7.1 | 7.07 | 6.3 | 7.2 | 8.3 |
% change | — | -19.08 | -33.2 | -0.68 | -10.8 | +14.3 | +15.3 |
Weavers | 16.0 | 16.0 | 13.0 | 12.0 | 11.0 | 10.0 | 10.0 |
% change | — | 0.0 | -18.8 | -7.7 | - 8.3 | -9.0 | 0.0 |
Spinners (males) | 24.0 | 23.0 | 22.0 | 21.0 | 20.0 | 20.0 | 20.0 |
% change | — | -4.4 | -4.3 | -4.5 | -4.7 | 0.0 | 0.0 |
Warper (female) | 10.0 | 9.0 | 8.0 | 7.0 | 7.0 | 7.0 | 7.0 |
% change | — | -10.0 | -11.1 | -12.5 | 0.0 | 0.0 | 0.0 |
Cutters (males) | 21.0 | 20.0 | 20.0 | 18.0 | 16.0 | 14.0 | 13.0 |
% change | — | -4.7 | 0.0 | -10.0 | -11.1 | -12.5 | - 7.2 |
Source: British Parliamentary Papers ; see text. |
sents the data for selected occupations, including the variations in wheat prices for the same intervals.
The percentage fall in wheat prices far surpassed the fall in wages through 1828, which suggests that the standard of living was improving.[164] This was valid even for weavers, who experienced the largest fall in wages of all listed woolworkers (-18.75 percent). Between 1829 and 1835, the fall in wheat prices slowed significantly, while wage rates declined at a faster pace for the first time. Between 1836 and 1838, the situation grew more critical. Wages continued to fall in 1837 and remained stationary in 1838, and for the first time, in 1837, wheat prices began to rise modestly.
The practice of paying in truck, which spread after 1825, compounded the decline of the standard of living in this latter period. Payment of wages in kind, or "truck," enabled the manufacturer to lower his workers' earnings indirectly by 15 or 20 percent.[165] He required workers to buy goods in his shop, or at one in which he held an interest. These goods sold at higher prices, were of inferior quality and were usually underweight. Although legislative measures were proposed to suppress the practice, such legislation was easily evaded; either penalties were too lenient, or proving any but the most flagrant violations became too difficult. Many of those successfully prosecuted at Horsley Petty Sessions were repeat offenders because fines were nominal. Most truck-sters, however, were too delicate in their proceedings to be found in technical violation of the law. "[The] workman earned his wages," one legal commentator observed, "under the impression created by the course of dealing that he was to lay out the same at some particular shop favoured by the manufacturer."[166] Noncom-pliance, or complaints regarding the inferiority and exorbitant prices of goods, would result in dismissal:
[If] they did [complain], the master would make but little reply; but, in a few days, or at the next settling, some trifling fault is found, or "not being in want of so many hands," they are turned off, but not a word is said about the shop. The workman is left to draw his own inference. The workmen know this and are therefore compelled. . . to submit to silence.[167]
Dealing in truck was more widespread during periods of economic depression, since less efficient manufacturers were desperate
to save their establishments by reducing labor costs; the existence of a surplus labor population facilitated their task. Because dealing in truck conferred a competitive advantage, it gave "respectable" manufacturers, who paid money wages, a reason to reduce their rates. The parliamentary commissioner estimated that one in five weavers in 1838 was paid in kind. Truck undoubtedly contributed to the general fall in wages in the post-1836 period. Public opinion, however, was against the practice, since it clearly enslaved and thoroughly demoralized the worker. Once economic conditions improved, the truckster enjoyed fewer opportunities, and because of the opprobrium of respectable society, he found plying his trade more difficult.
The parliamentary commissioner's wage series ends in 1838, but the fall in wage rates may have slowed during the prosperous years between 1843 and 1847. Improvement in the terms of trade, together with extensive outmigration in the previous period, should have enabled workers to command a better price. Wheat prices continued their linear decline, although at a slower rate; for the 1808-1849 period, the growth rate was -1.77 percent per annum. Wheat prices were slightly higher in the 1840s, but their advancement was too weak to alter the general trend significantly. Agitation for repealing the Corn Laws developed, nonetheless, in response to this slowdown. Since the clothiers found it in their interest to diffuse pressure for higher wages, the agitation revealed, indirectly, the extent of this pressure, which the Chartists had partly instigated. Scholars have generally regarded the mid-1840s as years of economic advance.[168]
In general, the trend in the standard of living of woolworkers, especially weavers, conformed to an apparent cyclical pattern. Deane and Cole were probably correct in suggesting that wages rose during the Napoleonic wars; the high wage levels, in the parliamentary commissioner's series, for the 1808-1816 period affirm their conclusion. Real wages suffered, however, since wheat prices rose proportionally higher.[169] Table 54 presents average wheat prices as a percentage of the average earnings of several categories of workers for each interval of the series.
For weavers and cutters especially, the price of wheat as a percentage of earnings moved full circle. For weavers, it was 82.3
TABLE 54. | |||||||
1808-1816 | 1817/18 | 1819-1828 | 1829-1835 | 1836 | 1837 | 1838 | |
Weavers | 82.3 | 66.6 | 54.6 | 58.9 | 57.3 | 72.0 | 83.0 |
Spinners | 54.8 | 46.3 | 32.3 | 33.6 | 31.5 | 36.0 | 41.5 |
Cutters | 62.7 | 53.3 | 35.5 | 39.3 | 39.4 | 51.4 | 63.8 |
Source: British Parliamentary Papers ; see text. |
percent in the 1808-1816 period and 83 percent in 1838; for cutters, it was 62.7 percent and 63.8 percent, respectively. This meant that the improvement in living standards occurred absolutely only between 1816 and 1828, and probably between 1843 and 1847, although the same hard evidence is lacking with respect to wages. The 1808-1816 period, moreover, was probably better than the year 1838; both intervals were marked by severe trade depressions, but the latter was compounded by the widespread payment of wages in kind. Wage rates probably never rose sufficiently to bridge the gap with rising productivity, even in the prosperous years of the mid-1840s and post-1850 period.[170] Insofar as the "quality of life" argument in the standard of living debate relates to the problem of exploitation,[171] we must conclude that the factory system produced a deleterious effect, despite the comparatively benign effect of cloth production on juvenile and adult mortality, as recorded in chapter 5.
Summary and Conclusion
The revolution in woolen manufacturing in the Stroud and lower districts of Uley, Dursley, and Wotton-under-Edge marked the transition from a protoindustrial to a factory-based system. The most distinguishing characteristic of this transition has been its comparative failure to revolutionize local society. Although improvements in communication (coupled with the growth of industry) fostered regionalism, significant urbanization did not take place, and a net loss of population occurred over the period.
Indeed, the cloth districts entered into decline virtually at the point of consolidation of the factory system, and contrary to the experience of the northern textile trade.
Excess capacity, induced by structural defects in the industry's power-supply system, rather than the alleged entrepreneurial failure of its clothiers, explained Gloucester's inability to remain competitive. Because of intensified competition and the vulnerability of smaller firms to trade depression, large capital-intensive firms came to predominate earlier at Gloucester, whereas a plethora of small firms coexisted with giant establishments at Yorkshire as late as mid-century. Gloucester's small firms did not necessarily operate inefficiently; large firms, because of greater capitalization, proved better equipped to glean greater shares of a declining market. After 1825, however, even this stratum began to experience a rising rate of bankruptcy and retirements from trade. The lower district collapsed as early as 1831 because concentration on coarse items brought it into direct competition with Yorkshire. Nailsworth declined more gradually because its unsurpassed fine cloths partially protected the locality from northern competition, but the loss of the coarse trade adversely affected it as well. Gloucester's woolen industry ultimately fell victim to market forces, and in this respect, its experience illustrates how contingency could accompany the process of modernization.[172]
Despite this failure, industrialization had an impact on labor that can be associated with a modernizing trend. The emergence of the factory system gradually undermined the protoindustrial household economy, in which each family member found a place in a delicately balanced internal division of labor. This picture of the protoindustrial household can be overdrawn, however, since it assumes the absence of traditional craft distinctions between master, journeyman, and apprentice, which, in fact persisted quite late. Still, the factory system induced "functional differentiation" in spinning and weaving, separating work from the home even when wives and children continued to labor elswehere.
Wives and daughters who spun or wove at home, following the emergence of the factory, engaged in a less synchronized work rhythm than their predominantly male factory counterparts. Moreover, as factory workers, women generally engaged in less skilled and comparatively less demanding occupations; nor did
they always work alongside other family members. A reconstitution of the family as a productive unit within the factory quite possibly occurred after midcentury; until 1850, however, this study affirms the traditional functionalist view.
Apart from its impact on the gender-based division of labor, the factory system greatly improved labor productivity, particularly among former journeymen and apprentices. More rigorous work discipline fostered habits of self-discipline and individual autonomy. Under then prevailing conditions of stagnation, however, the new regime also promoted exploitation. Falling. wage rates conspired with more intensive expenditure of effort and a slowdown in the rate of falling grain prices to produce a limited decline in living standards for the critical period of transition, from 1828 to 1842. Still, how artisans and industrial workers responded to the factory system, in the forms of strikes and protests, reveals the truly subjective side of the issue behind changing living standards and remains to be examined.